Consider the many virtues of valves.
They regulate temperature and prevent backflow contamination. Create precise mixtures. Control pressure and stress. Ensure safety in the event of system failure.
And yet, valves often are among the last considerations when designing an industrial piping system. One possible explanation: Valves are among the cheapest components to buy and install—leading many to underestimate their overall importance.
And yet installing the correct valves, made of the proper material in the right configuration will determine whether a system succeeds—or fails. Performs as you need—or represents a costly mistake.
We run through the most common valve configurations and how they work.
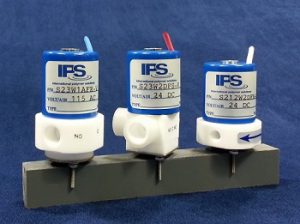
Solenoid: electro-mechanical valve consisting of a coil, plunger and sleeve assembly most commonly used to control the flow of liquid or gas. In a closed valve system, a spring holds the plunger in place to prevent flow. Once the solenoid coil is energized, the magnetic field raises the plunger to enable flow. The opposite is true in an open valve system.
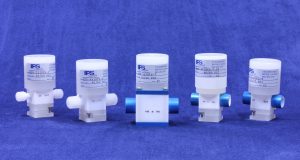
Pneumatic: used to control or modulate airflow. Common types of valves used within pneumatic systems include:
- Pressure Relief Valves control pressure by opening and closing the chamber through which pressurized air moves. Pressure relief valves are a fail-safe to prevent equipment failure.
- Flow Control Valves control air velocity from the actuator, the part within pneumatic systems that converts air pressure into motion.
- Quick Exhaust Valves consist of an input, an outlet and an exhaust to provide a rapid exhaust of controlled air.
- Directional Control Valves change the direction of pressurized air and show the number of positions, methods of actuation, number of ports and paths air can take.
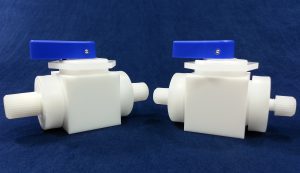
Manual: primarily used to stop and start flow through the use of a handwheel or lever. Common manual valves include:
- Ball: uses a pivoting ball to control liquid flowing through a system.
- Check: allows fluid to move only in one direction only, primarily to prevent backflow.
- Precision Plug: features a manual adjustment knob with fine threads to precisely set desired flow rate.
- Metering: uses a tapered plug-stem to finely adjust flow.
- Stopcock: features a handle that points in the direction of flow, often used for chemical fluid and gas shutoff.
- Diaphragm: features a flexible diaphragm for hard-seat seal and typically used where pneumatic and electrical connections are not practical or necessary.
The material used in constructing valves depends on the type of fluid or gas running through your industrial piping system.
When working with high alkaline media (high pH) or high acidic media (low pH), extra care must be taken, as depicted in the graphic. The pH Scale ranges from 0-14, with zero representing a highly acidic media and 14 representing a highly alkaline media. Both extremes can be very corrosive to piping, tubing, fittings, filters, pumps, tanks and valves. These types of systems typically require components constructed of high-purity polymer.
Valves perform essential functions in every industrial piping system. iPolymer’s knowledgeable staff has years of experience to help you get what you need. Give us a call at 435.783.6040 or request a free quote.











